Sulfur Guard™
Why You Need Pure Carbon Dioxide
To reduce batch contamination and product loss, you must use an effective H2S (Hydrogen Sulfide) for purification of CO2. Especially important in the food and beverage markets, pure CO2 protects your products from the risk of contamination by sulfur compounds, aromatic hydrocarbons, aldehydes and potentially harmful submicron particle contamination and bacteria. These contaminants may cause off-flavors and spoilage problems that can quickly translate into product and dollar loss.
You may not now be adequately protected. Sophisticated quality testing equipment has shown that the commonly used activated carbon filters do not always effectively achieve the high quality gas as recommended in the ISBT CO2 Guidelines. *
However, you can achieve this high level of purity when using a Sulfur Guard™ filter that incorporates a unique combination of adsorbents to remove the contaminants from CO2 that most threaten food and beverage quality. The use of effective, economical filtration media specifically designed for CO2 will help ensure that your product is protected from these contaminants. Below is an example of our typical five stage system that we use to to purify CO2 in beverage plants.
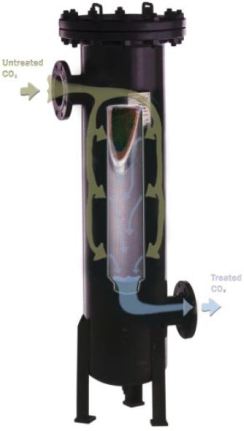
BA-Series filters may also be used in applications requiring compressed air to be free of odor or taste-bearing hydrocarbons. Food/beverage applications are an Example of where compressed air comes in contact with the product. The BA-Series can also be used as a prefilter for critical needs such as zero air generators, membrane filters and many others!
Replacement elements are supplied in convenient repair kits which include one coalescing element, two activated carbon adsorber elements, and replacement seals. Two adsorber elements are supplied because the stage one coalescer will routinely outlive the extremely sensitive second stage adsorber element.
Finite® also supplies pressure regulators which can be used downstream of the BA-Series to lower system operating pressures to desired levels for breathing air applications. Please refer to Finite® bulletin Finite®s pleated PTFE media has the the highest efficiency and lowest pressure drop at rated flow in the filtration industry. These important factors provide substantial savings to you, our customers.
All of the filter housings are constructed of 316L stainless steel and have a max. pressure rating of 150 PSIG/10 bar. Connection sizes range from 1” NPT – 6” flange.
How Micropure Does It Better
Sulfur Guard™ by MicroPure® purifies CO2 by removing sulfur compounds, aromatic hydrocarbons, and aldehydes plus other potential contaminants through chemical adsorption. Sulfur Guard™ has been designed specifically to adsorb the sulfur compounds, Hydrogen Sulfide (H2S) and the particularly troublesome Carbonyl Sulfide (COS) that can be unpredictably present in CO2. This special design also removes benzene, hexane, volatile oxygenated hydrocarbons, and some aldehydes more efficiently than traditional activated carbon filters. Under typical levels of contamination, the filter cartridges should be changed every six months.
The Sulfur Guard™ filtration mechanism is irreversible. Its formulation of filter adsorbents has special properties that when combined with activated carbon chemically converts H2S and COS into a stable form. This ensures that the adsorbed contaminants will not de-sorb back into the pure CO2 stream. Extensive testing both in the laboratory and in the field has shown that this technology is extremely effective. **
The adsorption filter is only part of the Sulfur Guard™ CO2 purification system. In addition to the sulfur- adsorbing filter stage there are other filter stages that include upstream coalescing filters to remove liquid water and oils and if desired, an additional activated carbon filter can be added upstream of the special Sulfur Guard™ stage to remove high levels of aromatic hydrocarbons. A final stage particulate filter will remove particles and bacteria down to the 0.01-micron level.
Sulfur Guard™ Presentation
Sulfur Guard™ offers a combination of features
Large Capacity Filter Element
- removes Carbonyl Sulfide and Hydrogen Sulfide
- also removes aromatic and volatile oxygenated hydrocarbons
- allows high CO2 flows at low pressure drop
- permits a much smaller sized filter when compared to traditional carbon filters
- filter media is completely contained in filter element - no loose carbon
Filter Housing Flexibility and Durability
- housing accommodates Coalescing, Activated Carbon, and Sulfur Guard™ stages
- all stainless steel, corrosion free design
- high strength ASME vessel
Filter Designed for Easy Maintenance
- easy top loading access to filter element for quick change
- no messy carbon to change
- lowest total maintenance costs
Filter Stages
Stage I – removes liquid water and oils
Stage II – removes aromatic hydrocarbons
Stage III – removes sulfur compounds, oxygenated aromatic hydrocarbons, and aldehydes
Stage IV – may be needed to remove carbon fines where traditional carbon bed filters are in use
Stage V – removes ultra fine particles including potentially harmful bacteria.
Technical Data
Maximum Operating Pressure | 325 psig / 22.4 barg |
Maximum Operating Temperature | 120 F° / 49 C° |
Maximum Intermittent Temperature | 250 F° / 121 C° |
Maximum Relative Humidity | 50% |
Materials of Construction: | |
Filter Housing | 304 SS |
Filter Element | Galvanized Carbon Steel & Polypropylene |
Gaskets | Fluoroelastomer |
Typical Applications
- Soft Drink Production Plant
- Beer Production Plant
- Soda Fountain or Beer Retail Points - of - Use
SulfurGuard Filter Time Interval Explanation
- Contaminants present in CO2 stream. Each application provides a different set of challenges. Each possible contaminant in the CO2 stream will present a different strain/workload for the filtration system.
- Contaminant percentage. The percentage or ppm level is factored into the life span of the filter. Each filter is rated to absorb a specific number of lbs. of a contaminant. If there is a higher level of the contaminant, then the life span will be shorter.
- Absorption factor of each element. This factor is given to us by the filter media components. We use a contaminant compatibility chart for each media. This chart will show each filter material and how much of a specific contaminant will be absorbed prior to material/filter failure.
- CO2 flow rate. The flow rate of the CO2 will have a similar effect on the life span as the contaminant percentage. The higher the flow rate/yearly consumption, the shorter the life span will be for each filter. The lower the flow rate/yearly consumption, the longer the life span will be for the filter.
- Pressure. Pressure does not affect the lifespan of the filter.
- Temperature. Temperature does not affect the lifespan of the filter. The Filters have a max Temperature of 225°F
Typical Application set up is a 5 stage setup. There are multiple filter sizes and connections available for your system. In this article, we will focus on the 2 most common sizes. There are sizes above and below what is listed in this explanation.
Stage | Filter Type | Filter Series | Purpose |
1 | Coalescing | CFCC | Removal of Liquid and oils |
2 | Activated Carbon | CG | Absorption of aromatic carbon based contaminants |
3 | SulfurGuard | SG | Absorption of sulfides |
4 | Particulate | CFCC | Particulate filter |
5 | Sterile | PSF | Sterilization of Gas for acceptable use in food and beverage application |
The CFCC series filter (stage 1 & 4) works much like a screen and is installed to remove liquid and particulate (0.01 micron). This filter does not carry a specific hour or flow change out rate because it is does not fail based on absorption. The failure would come from overloading of Particulate or liquid. Because there is no specific failure rate, we include a differential gauge with the filter to properly manage filter life. In food and beverage applications, we recommend that this filter is changed out roughly once a year. In situations where the incoming CO2 is extremely dirty, we have seen the need for a 6 month change out, but that in not common. The 6 month change out is more common in non-USA installations where incoming CO2 quality is questionable. Our rule of thumb is to replace this filter when the other 2 phases are changed out. The most accurate way to measure change out would be PSID of filter. When the PSID gets to an unacceptable rate for your application, replacement is recommended. Typical dry PSID of filter is around 1 PSID. A PSID of 3 is common with 10-20 wt. oil.