The Highs and Lows of Fermentation Filtration
The Client:
A large fermentation facility in Mexico. The facility is owned and operated by one of the worlds largest chemical engineering and supply companies.
The Problem:
The fermentation process requires steam in multiple areas. The fermentation process of this application requires the air to be a certain temperature and humidity level to spur growth of the product. Steam is injected into the air stream to ensure the air is at the correct temperature and humidity level. The fermentation process would negatively effected if contaminants from the steam system were introduced to the air stream. After the fermentation process is run, steam is used to clean all the tanks and piping throughout the process to ensure all possible bacteria or contaminants are removed.
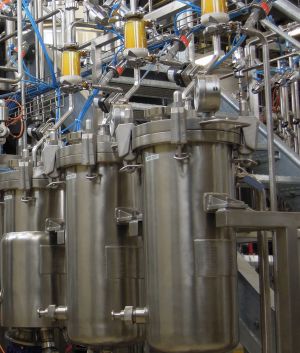
The Process:
There were several unique problems that this application provided to the client. The first was the high flow rate of steam needed for the fermentation process as well as the sanitation process. The high flow was combined with a low pressure. This combination requires that several very large filters be used to properly filter all the steam. The second problem was that process also required very large process connections to fit into the already piped system. The third was the space in which steam filtration system must be installed. Since this facility was already intact and operational, there was not a large open space to install a filtration system. Typically in these situations, multiple filters in series would be installed to handle the flow rate and give the customer a solution. This was not possible because of the small space available.
The Solution:
The engineers approached the client with a solution that would fit their specific need of high quality filtration at the high flow rate they need without the need of a large footprint. The newly designed PDF multi-round filter series was the best solution to the application at hand.The solution Micropure was able to supply was a larger housing that would be able to fit multiple elements inside each housing. This allowed for a extremely high flow rate through a single housing. The single housing offered a small footprint with the ability to have large connections sizes for the inlet and outlet piping. In this specifc application, the housing contained three 140 mm elements instead of the standard 1 element per housing. By using the segmented element design, the client was still able to achieve an extremely low pressure drop across the filter. This allowed the low pressure steam to be used without worry about any sort of pressure loss post filter effecting the application.
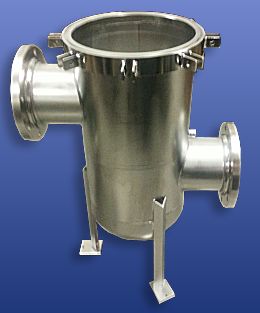