Mash Press
What’s a Mash Press?
A mash filter press is a large frame filter used for filtering mash. The mash goes through the same basic steps as a traditional lauter tun. The mash is pumped into the filter. The mash slowly fills up each chamber. Once the chambers are filled to capacity, a squeezing process begins to help remove wort and extract from the mash. Pressure from the mash and squeezing process will push the wort through a micron rated filter cloth before the wort gets pumped to the next phase.
Ask Micropure about a Mash Press
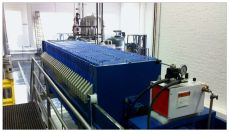
Filter Press consisting of a series of cloth filters fixed to frames, used for the large-scale filtration of liquid under pressure.
Why use a Mash Press?
In a traditional brewery, a lauter tun is used to remove the wort from the mash & grains. A lauter tun removes the extract via gravity and circulation. In the lauter tun there is a false bottom with a screen. The mash falls to the bottom of the tank and is circulated by a rake. Mash build up on the bottom creates a filtration medium. This allows the solids and liquid (clear wort) to separate.
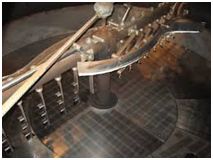
Rake system and False bottom that are common in commercial lauter tun
Why is the Mash Filter Press more effective?
- Achieve up to 98+% extract
- Produce faster conversion with fine stripping mill (up to 20% flour)
- 20%-40% combined overall raw material, energy and labor cost savings.
- Flexible System that allows for multiple brew styles
- High Degree of Automation Expandable system
Advantages of Membrane Filter Plates
Shorter Filtration Cycles
- The squeeze feature of the membrane plates allows you to shorten your cycle time between loads
Lower Residual Moisture in Cake
- By using feed and squeeze pressure, you dramatically reduce the amount of moisture in the cake. This makes the waste load from your press smaller lighter.
Lower pressure to be used on plates
- By adding the squeezing of the membrane plates, you do not have to run your filter press feed pressure as high as in a standard membrane press.
Higher Volume per Chamber
- By Squeezing the mash, you have the ability to fit more mash into the system then with a traditional press.
Shorter Filter Press Frames
- Membrane filter presses have deeper chamber depths allowing you to have less chambers per hectoliter compared to a non-membrane filter press.
Phases of Mash Filter Press Cycle
1 - Filling Stage
Filling Stage: The Mash enters the chambers through a feed pump.
2 - Filtration Stage
Filtration Stage: Once the chambers are full, the Mash that is being pushed by the feed pump will force the Wort out from the chambers. The Filter Plates and Filter Cloths will capture the Mash Grains.
3 - Compression Stage
Compression Stage: Once the feed pressure has cycled out, the system will be closed and the membrane squeeze will begin. Water or Air is pumped behind the membrane bladders. This compress the mash grains inside the chambers and forces out more Wort.
4 - Draining Stage
Draining Stage: Once the compression stage is complete. The Water or Air will drain from the Mash Filter.
5 - Discharge Stage
Grain / Cake Discharge Stage: Each chamber is opened up for cleaning and the grain is discharged.
Choosing a brewing production system is a difficult task. Speak with Micropure about how a Mash Press can be integrated into your brewery.
Ask Micropure about a Mash Press
Technical Specs
Maximum Feed Pressure | 100 psig |
Maximum Squeeze Pressure | 100 psig |
Maximum operating temp | 200°F/121°C |
Mash Press Sizes | 1 HL-200HL |
Pore Sizes | 0.5 um – 200 um |
Material of Construction: | |
Frame | Carbon Steel |
Filter Plates | Polypropylene |
Membrane Bladder | EPDM |
Filter Cloths | Polypropylene |