CO2 safety is number one with Sulfurguard
The Client:
A world renowned beverage and soft drink manufacturer that is opening a new facility in the Middle East. As part of the carbonation process, the plant uses roughly 6,000 metric tons of CO2 per year. Their process uses a flow rate of 1500 kg/hr at 20 bar pressure.
The Problem:
Since the late 90’s, every carbonated soft drink manufacturer has been concerned with the quality and sterility of the CO2 that is used for the carbonation of their products. Coca Cola’s Recall of 30 million cans and bottles in 1999* showed how harmful CO2 contamination can be for human consumption and how the resulting recall and product loss can affect the yearly financials of the overall company**. The new facility that the client is opening wants to ensure the sterility of its CO2 supply along with making sure that they have a cost efficient filtration system. They are extremely interested in getting a filtration system that has low replacement costs and long lasting filtration elements.
The Process:
The Engineers at Micropure reviewed the specific application and needs of the client and their new facility. Micropure presented them with a proposal for its patented SulfurGuard CO2 filtration system. The Sulfur Guard system has the ability to be sized to fit the client’s needs. The proposal to the client shows the sizing and basic technical capabilities as well as the specific replacement intervals.
Phase 1:
Removal of particles and
oil droplets down to 0.01 micron
Phase 2:
Removal of
aromatic hydrocarbons
Phase 3:
Removal of sulfur compounds,
oxygenated aromatic
hydrocarbons and aldehydes
Phase 4:
Removal of all particles down
to 0.1 micron as well as
any bacteria in the stream
The Solution:
The patented SulfurGuard CO2 filtration system puts the process gas through several phases to ensure the post filtered CO2 is 100% sterile, free of any possible contaminants and safe for use in soft drink carbonation. The first stage is an oil and liquid coalescing phase that removes particles and oil droplets down to .01 micron. The second phase removes any aromatic hydrocarbons that are present in the CO2 stream. In the third stage, the filter will remove sulfur compounds, oxygenated aromatic hydrocarbons and aldehydes. The final stage, usually installed after the carbonators, is the sterile filter. This filter will remove all particles down to .1 micron as well as any bacteria that may have been present in the CO2 stream. Having these phases present in a system ensures that the filtered CO2 is 100% safe for use in carbonation and human consumption.
In this specific application, Micropure recommended that that client install a SulfurGuard system with 8” stainless steel vessels and 28” elements. This system will give the client a long replacement interval as well as low pressure drop from one phase to another. The top loading design allows for quick and simple filter element change out saving valuable production time. Since each phase is contained in a gasketed element, there is no messy carbon to deal with during the filter change out. All of these factors allowed the customer to receive the best system for their application. The client received a system with low pressure drop, high quality filtration, low replacement costs and long replacement intervals.
*Victoria Johnson and Spero C. Peppas “Crisis management in Belgium: the case of Coca-Cola” (Corporate Communications: An International Journal, Volume 8 . Number 1 . 2003 . 18-22)
**Coca-Cola Earnings Fall 21%, Reflecting Troubles in Europe By CONSTANCE L. HAYS Published: July 16, 1999
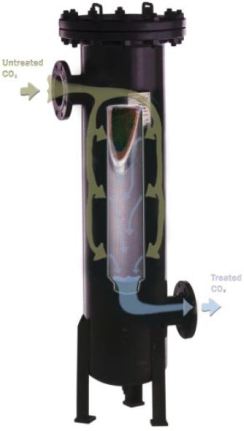