Cleaning Up Open Fermentation
The Client:
A craft brewery in British Columbia, Canada. The brewery was started in 2008 and has grown steadily since its inception. They are now distributing their beer through British Columbia and the northwest corner of the USA.
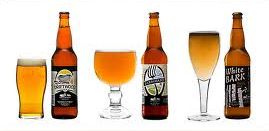
The Problem:
Typically, Breweries use compressed air or medical grade oxygen to aerate the wort and start the fermentation process. This process is typically done in a closed or pressurized environment to avoid any issues with contamination from the air in the brewing facility. The client decided they were going to aerate the wort and ferment their beer through a process called “Open Fermentation”. In this process, the tank would have an opening at the top to allow for access for air into and out of the tank. This process was typical in the days prior to airlocks and cylindrical tanks. This process allows the wort/beer to breath naturally throughout the fermentation process. Brewers choose this method because they believe they can achieve more complex taste profiles with this process.There two issues to consider with this method. First, by leaving an open port on the top of your tank, you have to chance to contaminate your batch of beer by letting regular plant air into your tank. Depending on where this tank is in your facility, there are a variety of possible contaminates that could enter the tank. If you choose to put some sort of protective filter on the tank, your concern is the length of time you product is in the tank and how long a filter would need to be working prior to regeneration or replacement. Both of these play into your decision to use open fermentation and what filter you use to protect the incoming air supply.
The Process:
The Engineers at Micropure reviewed the application parameters and what the brewery was trying to accomplish with this process. Micropure put together a proposal for a sterile tank vent filter that could allow the tank to breathe while ensuring the air entering the tank would be sterile and clean.
The Solution:
Micropure’s engineers typically offer a small compressed sterile air filters for wort aeration and fermentation applications. This filter type would not work for the application because there was no pressurized airline going to the tank. Instead Micropure offered a Sterile Tank Vent filter. The Sterile Tank vent filter is simply attached to the top of the tank via a basic pipe fitting (NPT, Tri-Clamp, etc.). By using a Sterile Tank Vent filter, this allowed the air to move freely out of the tank when a new batch of wort entered the tank. It also sterilized the incoming tank air when it was needed in the fermentation process. This two way flow is only possible because of Micropure’s Bi-directional flow media. The second concern was solved by the high quality filtration media. Micropure uses segmented filtration allowing each media discs used in this filter application act independently creating an extremely low pressure drop and long life span. The long life span of the filter allows the brewery to leave the tank vent filter installed for the entire length of the fermentation process with the need of cleaning or regeneration. Cleaning can tank place after fermentation cycles is complete. Cleaning and Regeneration is a simple short process that can be completed prior to getting the next batch of wort into the fermentation tank.
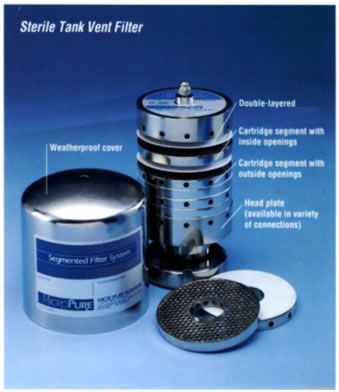